Friction Materials
Brake Pad Compressibility
The brake pad compressibility is a key design parameter of brake systems and can impact brake performance and comfort, as well as noise and vibration occurrences. Only a few formulation components can influence the pad compressibility directly and consistency is essential to ensure that the compressibility is within the narrow ranges of the pad specification. Superior Graphite developed different grades of Resilient Graphite, tailored to increase compressibility to different levels in a consistent and controlled way. The Resilient Graphitic Carbons (RGC™) and the Artificial Resilient Graphite (ARG™) are performance additives for the highest compressibility ranges (as shown in Figure 1), whereas the High Resilient Synthetic (HRS™) and Carbons (HRC™) are excellent alternatives for intermediate compressibility levels.
FIG. 01
Brake pad compressibility increase in an NAO formula with RGC™ and ARG™ as replacement of synthetic graphite (baseline)
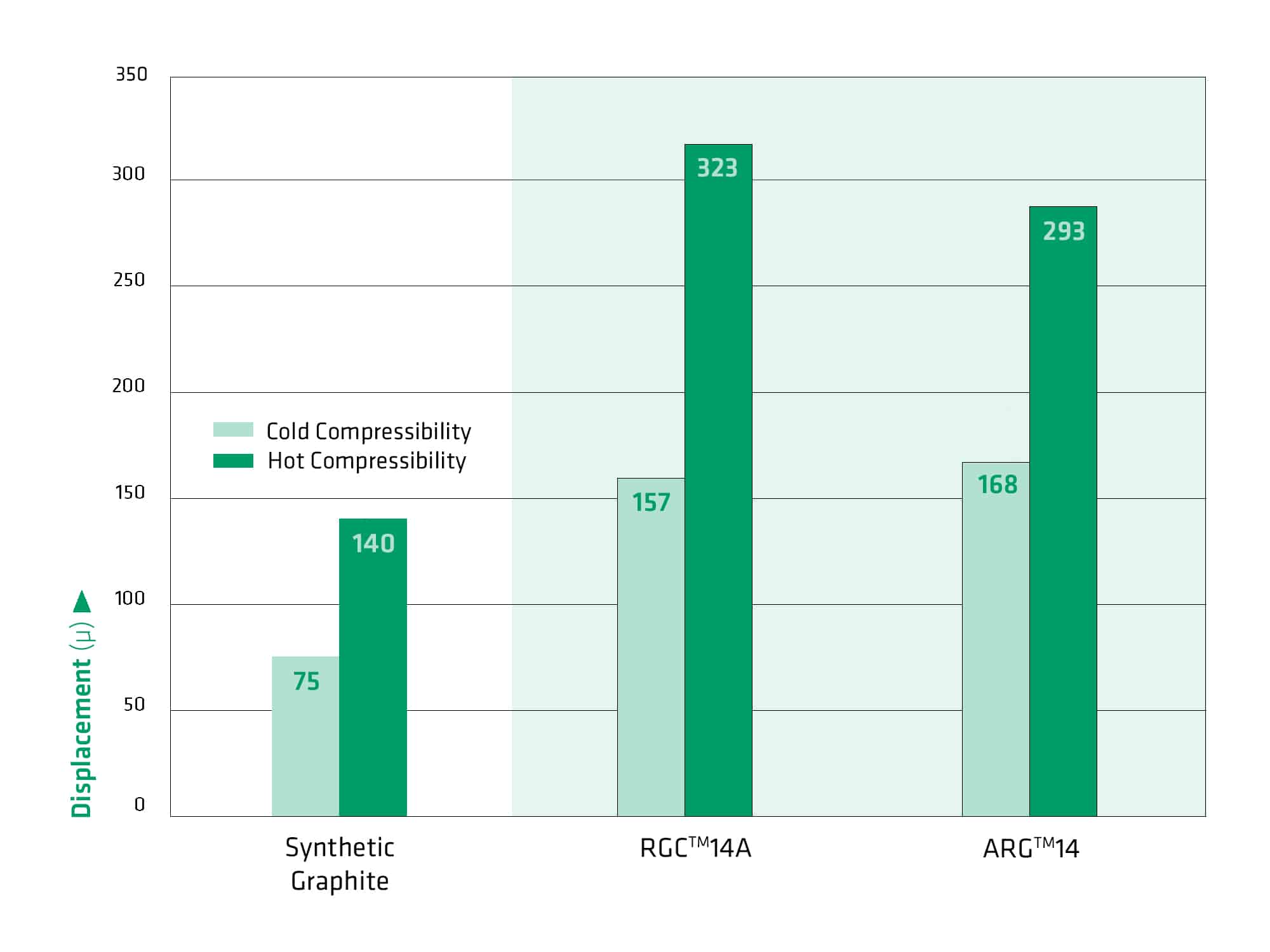
How can we help address your challenges?
Issue
Formulators have difficulties adjusting the compressibility of pads and this may negatively impact brake comfort and can cause unwanted vibrations, which can result in excessive noise while braking.
Solution
The Resilient Graphite grades are a proven solution to increase cold and hot compressibility due to their high resiliency. RGC™ and ARG™ exhibit increased porosity and resiliency which assist in adjusting pad compressibility and its open surface porosity promotes a strong bond with the phenolic matrix, resulting in the reduction of fading, especially at high temperature. Intermediate compressibility levels can also be achieved using Resilient Graphite grades in intermediate levels of resiliency, such as the High Resilient Synthetic (HRSTM) and the High Resilient Carbons (HRCTM).
Issue
The brake pad compressibility is specified in narrow ranges and keeping this parameter controlled within those limits is a challenge for the formulators.
Solution
The Resilient Graphite grades also contribute to keeping compressibility within the narrow specified ranges due to the material property consistency achieved using Superior Graphite’s processing capabilities for purification, graphitization and sizing of the products in the FormulaFX portfolio.
FormulaFX™ Benefits:
Increases brake pad compressibility
Noise and vibration reduction
Friction stability enhancement
Pad wear minimization

To learn more about FormulaFX™ click here.
Let’s discuss your application and your specific product needs.
Contact Us