Friction Materials
Copper Free Formulations
Copper was widely used in brake pads mainly due to its contribution to heat dissipation and reduction of noise and vibration. Due to environmental and health reasons, there have been progressive copper reduction initiatives in the US since 2010, resulting in the current maximum limit of 0.5% of copper in brake pads. This regulatory aspect has already affected the market globally and there is a trend of increasing concern with brake particle emissions and their toxicity in upcoming regulations. Graphite has high thermal conductivity and is considered a potential replacement for copper to keep heat dissipation within targets. The Resilient Graphite grades from Superior Graphite also contribute to noise and vibration reduction. Therefore, the Resilient Graphitic Carbons (RGC™) and the Artificial Resilient Graphite (ARG™) are excellent candidates for a smooth transition to copper free formulas, keeping the desired levels of noise/vibration and heat dissipation for optimal performance.
FIG. 1
Properties of Graphite
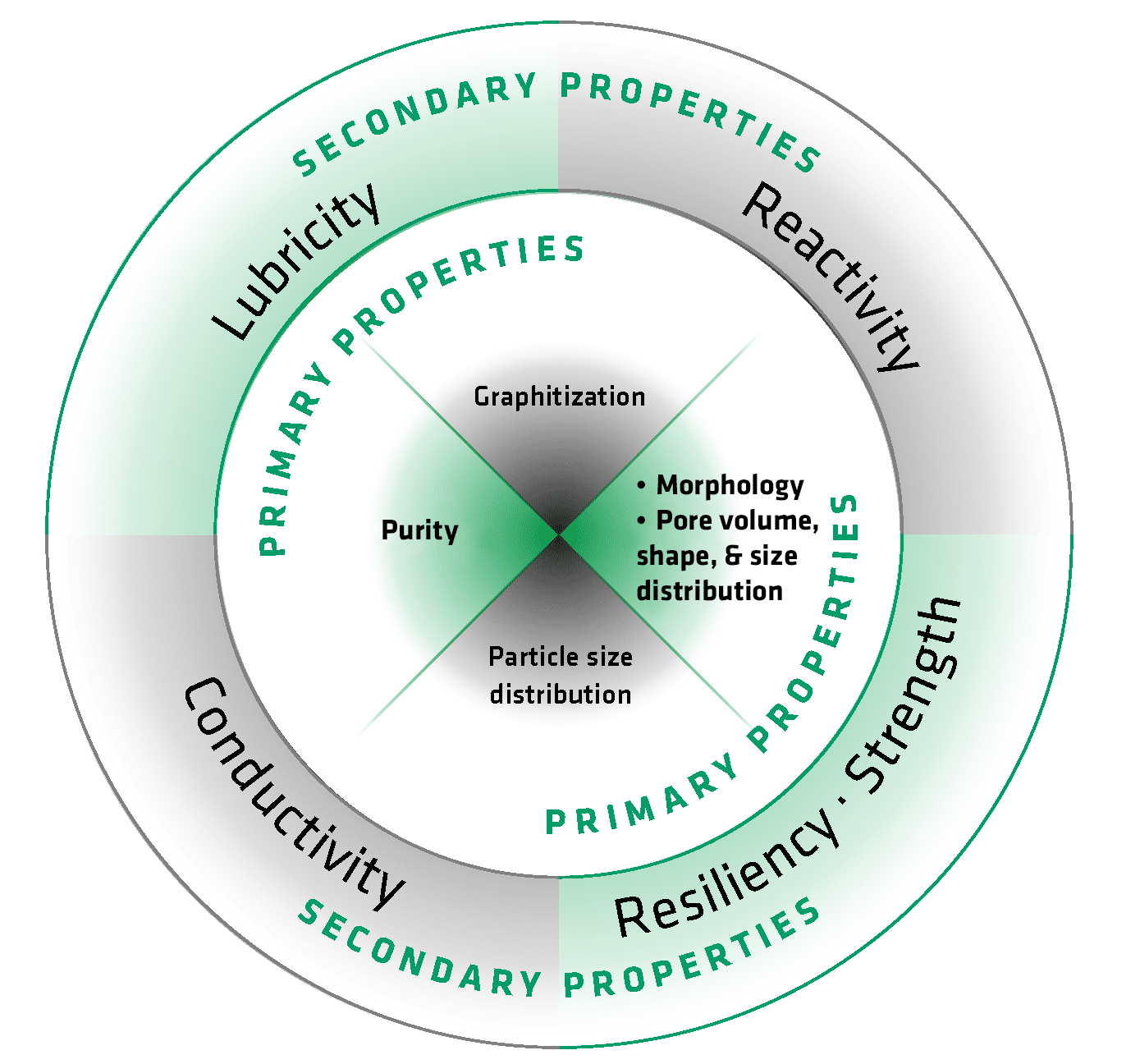
How can we help address your challenges?
Issue
The copper restriction in automotive brake pads was already implemented in the US and this regulatory trend tends to spread globally. The copper free brake pads exhibit decreased thermal conductivity, causing difficulties in heat dissipation which is essential for proper, safe and consistent brake operation.
Solution
Graphite is well known for its thermal conductivity properties and is therefore considered a potential replacement for copper. Several primary properties of graphite (Fig. 01), such as morphology, purity, degree of graphitization, porosity or particle size distribution, contribute to thermal dissipation. Specialty engineered graphitic materials like the Resilient Graphitic Carbons (RGC™) and the Artificial Resilient Graphite (ARG™) enhance thermal conductivity in brake pads due to their higher porosity.
Issue
Copper was also used in brake pads to help control the occurrence of noise and vibrations during the brake applications.
Solution
The high resiliency of the Resilient Graphitic Carbons (RGC™) and the Artificial Resilient Graphite (ARG™) contributes significantly for brake pad compressibility increase, which results in the reduction of noise and vibration while braking. Therefore, the Resilient Graphite grades from Superior Graphite are excellent candidates for controlling the noise transition to copper free brake pads.
FormulaFX™ Benefits:
Contributes to heat dissipation
Increases brake pad compressibility
Noise and vibration reduction
Pad wear minimization

To learn more about FormulaFX™ click here.
Let’s discuss your application and your specific product needs.
Contact Us